Что такое ультразвуковой контроль?
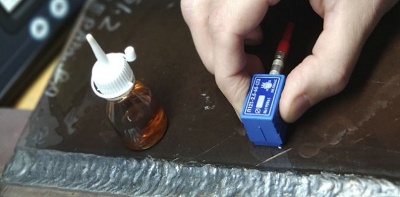
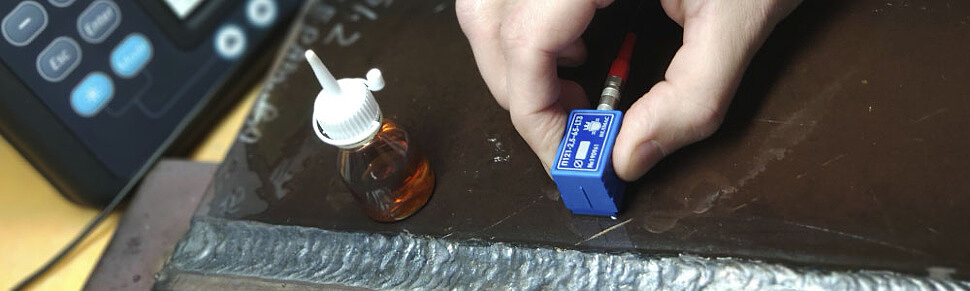
Ультразвуковой контроль (далее – УЗК) – это обобщённое название группы методов неразрушающей диагностики материалов и изделий, без нанесения повреждений исследуемому предмету. Методы основаны на способности всех материалов проводить звук. Общий принцип методов УЗК состоит в том, что в контролируемый предмет вводится звуковой импульс, который распространяется в материале, отражается от границ и внутренних нарушений сплошности материала, затем принимается. По параметрам принятого сигнала можно судить о наличии и расположении и размере несплошностей материала, а также о физических свойствах самого материала. Методы УЗК применяются для обнаружения дефектов в различных материалах, измерения геометрических параметров изделия, измерения твёрдости металлов и пластиков.
В группу методов ультразвукового контроля входит ультразвуковая дефектоскопия – это общее название группы методов УЗК, направленных конкретно на обнаружение и измерение параметров дефектов материала. Основоположником является Сергей Яковлевич Соколов, который в 1928 году запатентовал способ обнаружения нарушений сплошности в металлах при помощи ультразвуковых колебаний. Он разработал первые ультразвуковые дефектоскопы и основал кафедру электроакустики и ультразвуковой техники в Ленинградском Электротехническом Институте.
- Методы контроля
- Преимущества и недостатки
- Виды УЗК
- Объекты УЗК
- Государственные стандарты в области ультразвукового контроля
Методы контроля
Методы УЗК считаются неразрушающим и не повреждающим способом диагностики состояния объекта. Это связано с тем, что они не требуют вскрытия (разрыва, излома, разрезания) объекта, а позволяют визуализировать внутреннюю структуру материала без нарушения его целостности. В подавляющем большинстве случаев кратковременное воздействие звуковых колебаний, используемых при контроле не приводит к появлению макро или микродефектов. При всех методах УЗК примеряются звуковые волны высокой частоты, которые не воспринимаются человеческим ухом – от 20 килогерц до нескольких десятков мегагерц.
Преимущества и недостатки
Преимущества метода:
- не оказывает разрушающего или повреждающего действия на контролируемое изделие;
- применяемые частоты и интенсивности ультразвуковых колебаний безопасны для оператора в отличии, например, от рентгеновского метода контроля;
- ультразвуком можно проверить большинство твёрдых материалов – чёрные и цветные металлы, пластмассы, композитные пластины и т.п.;
- современные приборы для УЗК имеют небольшие габариты и аккумуляторные батареи большой ёмкости, благодаря чему возможен контроль в труднодоступных местах и удалённо от электросети. Многие приборы выпускаются в пылевлагозащищённом и морозоустойчивом исполнении.
Недостатки метода:
- ввод ультразвуковых волн требует тщательной зачистки поверхности объекта, а также применения специальной контактной смазки;
- в результате прозвучивания измеряются не истинные, а условные или эквивалентные размеры дефектов, допустимость которых оценивается по специальным утверждённым методикам;
- требуется высокая квалификация персонала: для понимания изображения на экране дефектоскопа требуется специальная подготовка, в настоящее время действует система обучения и аттестации дефектоскопистов по 3 уровням квалификации.
Виды УЗК
Основными видами УЗК являются:
- дефектоскопия – методы выявления наличия дефектов, измерения их параметров с целью оценки опасности этих дефектов;
- толщинометрия – методы измерения остаточной толщины изделий, подвергающихся коррозии;
- ультразвуковой контроль свойств материала – совокупность методов контроля твёрдости, шероховатости, акустическая микроскопия и другие специальные виды диагностики.
Каждый из этих видов контроля требует специального обучения дефектоскопистов, а сам контроль проводится согласно действующим нормативным документам – ГОСТам, методикам, инструкциям и т.п.
Аппаратура для ультразвукового контроля:
- ультразвуковой дефектоскоп – электронный прибор, служащий для генерации электрических импульсов, приёма, обработки и визуализации результата;
- ультразвуковой преобразователь – специальный датчик, который оператор прижимает к объекту контроля. При излучении он превращает электрический импульс с дефектоскопа в ультразвуковой сигнал, который далее распространяется в объекте, а при приёме он наоборот превращает принятые звуковые сигналы в электрические, которые затем обрабатываются прибором. Существует большое количество типов и видов ультразвуковых преобразователей, которые выбираются в зависимости от объекта контроля и вида обнаруживаемых дефектов. Наиболее распространены пьезоэлектрические и электромагнитноакустические преобразователи;
- соединительные кабели – служат для подключения датчика к прибору;
- меры и настроечные образцы – изделия, которые содержат искусственный дефект и служат для калибровки дефектоскопа перед проведением контроля;
- контактные смазки – жидкости и гели, которые наносят на поверхность объекта, для того, чтобы улучшить условия перехода ультразвукового импульса из преобразователя в объект контроля;
- сканирующие устройства – различные вспомогательные механические устройства для удержания и перемещения преобразователя по поверхности объекта.
Объекты УЗК
При помощи УЗК контролируют практически все твёрдые материлы – чёрные и цветные металлы, литые и композитные пластики, бетоны, клееные и сотовые конструкции.
Главным ограничением на возможность УЗК являются естественные неоднородности материала: графитовые зёрна в чугуне, размер ячеек сотовых конструкций, или толщина слоя в композитных пластинах. Для контроля таких материалов выбирают
достаточно большую длину ультразвуковой волны, которая не будет отражаться от данных естественых неоднородностей, но будет чувствительна к подлежащим выявлению дефектам.
В общем случае можно считать, что в материалах, имеющих собственную несплошность структуры возможно выявлять дефекты, размер которых превышает размер структурных неоднородностей материала в 10 и более раз.
Наиболее частыми объектами УЗК являются:
Сварные швы трубопроводов и листовых материалов.
Сварной шов всегда имеет меньшую прочность, чем основной металл сваренных элементов, поэтому критически важно, чтобы в нём не было дефектов, дополнительно снижающих его прочность. При помощи УЗК в сварных швах выявляют трещины, непровары, свищи, пористость и другие виды дефектов. Ультразвуком контролируют магистральные газопроводы и нефтепроводы (в том числе из полиэтилена), технологические трубопроводы в химической и энергетической отраслях, резервуары, детали грузоподъёмных машин и т.п. Возможна диагностика всех видов сварных швов – стыковых, тавровых, нахлёсточных, а также точечной сварки.
Металлургические заготовки, литьё и поковки.
Заготовки могут иметь дефекты типа раковин, пор, трещин и других. Их необходимо выявлять при помощи УЗК, чтобы избежать расходов на дальнейшую обработку заготовки с дефектами, которые при обработке могут развиться в дефекты готового изделия.
Листовой прокат.
Этот вид заготовок чаще всего содержит дефекты типа расслоения – плоские тонкие нарушения сплошности, расположенные в средней части листа и значительно ослабляющие его прочность. Ультразвуковой контроль листового проката был исторически первым видом УЗК, который проводил С.Я.Соколов. В силу больших размеров контролируемых листов, этот вид контроля сейчас проводится на крупных автоматизированных установках прямо на металлургических комбинатах.
Железнодорожные рельсы, колёсные пары, оси.
При прохождении железнодорожных составов рельсы и колёсные пары подвергаются циклическим нагрузкам, в результате которых возникают трещины и иные виды эксплуатационных дефектов. УЗК рельсов проводится при помощи дефектоскопных тележек и автоматизированных вагонов-дефектоскопов. УЗК колёс, осей и колёсных пар проводится как вручную, так и на специальных автоматизированных стендах.
Бетонные и железобетонные конструкции.
Ультразвуковой контроль прочности бетона является лучшей альтернативой разрушающим методам контроля бетона. Существует хорошая отечественная аппаратура как для измерения прочности твёрдого бетона, так и для выявления внутренних дефектов в бетонных конструкциях;
Государственные стандарты в области ультразвукового контроля
УЗК почти всегда связан с диагностикой состояния опасных объектов, и проводится с целью предотвращения техногенной аварии. Поэтому методы контроля, требования к аппаратуре, порядок проведения и подлежащие УЗК объекты описаны в государственных и отраслевых стандартах, методиках, инструкциях и руководствах. Перечислить всю действующую нормативную документацию по УЗК в данной статье не является возможным, но отметим наиболее значимые ГОСТ, лежащие в основании системы стандартов в ультразвуковой дефектоскопии.
- ГОСТ Р ИСО 5577-2009 содержит определения всех терминов и понятий, принятых в практике ультразвукового контроля;
- ГОСТ Р 55724-2013 прописывает общий порядок контроля сварных швов различного назначения;
- ГОСТ 18576-96 содержит указания о порядке контроля железнодорожных рельсов;
- ГОСТ 24507-80 описывает контроль поковок;
- ГОСТ 17624-87 раскрывает метод контроля прочности бетона;
- ГОСТ 28831-90 описывает методы дефектоскопии листового проката;
- ГОСТ Р 55809-2013 раскрывает требования к ультразвуковым дефектоскопам и методы измерения их параметров;
- ГОСТ Р 55614-2013 регламентирует общие технические требования к ультразвуковым толщиномерам;
- ГОСТ Р 55725-2013 и ГОСТ Р 55808-2013 предъявляет требования к ультразвуковым преобразователям и задаёт способы измерения их параметров.